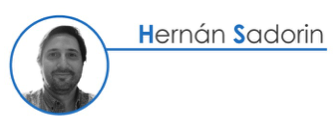
Industria 4.0 – Introducción
A lo largo de la historia, hemos transcurrido por tres de las llamadas “revoluciones industriales” (máquina de vapor/mecanización, energía eléctrica/producción en masa, automatización/electrónica/informática).
Actualmente nos encontramos transitando hace algunos años lo que se conoce como la 4ta. revolución industrial o “Industria 4.0”. Esto hace referencia al modelo de industria inteligente, en el cual dispositivos y sistemas interactúan con procesos físicos tomando decisiones descentralizadas. Los procesos, máquinas y componentes se comunican en tiempo real entre sí y con clientes, usuarios y proveedores. Este paradigma puede ser posible a través de “habilitadores digitales” que permiten la vinculación y comunicación entre lo físico y lo virtual/digital:
- Simulación
- Manufactura aditiva
- Ciberseguridad
- Realidad Aumentada (RA)
- Computación en la nube
- Robótica
- Internet de las cosas (IoT)
- Big Data
Si bien recientemente el tema de “Industria 4.0” comenzó a ser un tema muy divulgado de manera masiva, es importante destacar que muchos de los habilitadores digitales no son desarrollos recientes, sino que ya llevan sus años en el mercado. Por citar algunos ejemplos de dispositivos/conceptos que se desarrollaron a partir de la década de 1960’, tenemos al PLC (forma parte del habilitador “Internet de las cosas”), a los robots o a la inteligencia artificial. La particularidad que se está dando en los tiempos en los que vivimos es que, como todo desarrollo, los costos actuales permiten una implementación industrial cada vez más masiva y, por otro lado, los avances a nivel informático permiten una interconectividad entre los habilitadores que no tiene precedentes.
Industria 4.0 y Mantenimiento
Sin lugar a dudas, el mantenimiento de los activos físicos no escapa a esta “ola digital” que atraviesa toda la industria. Los habilitadores digitales disponibles en el mercado están abriendo un abanico de posibilidades para las personas que tienen la responsabilidad de mantener los equipos, principalmente brindando nuevas tecnologías de mantenimiento predictivo (mantenimiento en el cual se mide un parámetro y en función del resultado de la medición se deja operando al equipo o se lo interviene para realizar una reparación).
A continuación enumeramos algunas implementaciones que se pueden observar en la industria, aplicadas en el mantenimiento:
- Instalación de sensores que permiten el monitoreo continuo de variables (temperatura, presión, caudal, etc.), las cuales pueden observarse en planta o en dispositivos móviles y accionar sobre los equipos (de manera manual o automáticamente en función de algoritmos) de manera remota en función de los resultados.
- Utilización de anteojos con cámara para realizar inspecciones y que las mismas sean visualizadas por el resto del equipo o por algún especialista en cualquier parte del mundo.
- Utilización de drones con cámaras para realizar inspecciones en equipos con difícil acceso.
- Simulación de desgaste de componentes de equipos a través de un software.
- Implementación de un “Gemelo digital” (digital twin) de la planta.
Estrategias de Mantenimiento y Tecnología
Para las personas que gestionan el mantenimiento de los activos, es importante no dejarse “nublar” por estas nuevas tecnologías y no olvidarse que la responsabilidad principal por el funcionamiento de los equipos es de ellos, y no de las empresas que ofrecen los dispositivos tecnológicos. Es importante remarcar esto, porque:
- Los usuarios (empresas que gestionan los activos) son los que más saben sobre los equipos que tienen que mantener
- Los usuarios (empresas que gestionan los activos) conocen el contexto operacional en el cual el equipo va a operar
La presencia y disponibilidad de tecnología es importante y hay que aprovecharla a través del conocimiento de qué tecnologías existen y cuáles podrían aplicarse en los equipos bajo su gestión.
No obstante, las estrategias de mantenimiento deben ser desarrolladas por la empresa en función del conocimiento del comportamiento de las fallas (normalmente a través de la realización de un AMFE – Análisis de Modo de Falla y Efectos) y no en función de las tecnologías disponibles en el mercado. Qué mantenimiento realizar a un equipo, a qué frecuencia y por quien deben ser parámetros definidos por el usuario del equipo.
En nuestra experiencia, nos encontramos con empresas que compran dispositivos muy costosos con el objetivo de realizar un monitoreo de alguna variable de un equipo y:
– desconocen qué hacer con los resultados de ese monitoreo o;
– desconocen la frecuencia a la cual debería realizarse el monitoreo
Estas situaciones dejan en evidencia la implementación de una tecnología nueva sin contar con las estrategias de mantenimiento del equipo bien definidas. Esto puede llevar a una inversión sub-aprovechada o a tomar decisiones que no tienen que ver con la costo-eficacia sino con la disponibilidad de datos.