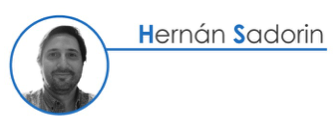
Introducción
Cuando los Equipos de trabajo que se dedican a la gestión de activos físicos (generalmente personal de sectores Mantenimiento, Operaciones, Ingeniería de Confiabilidad, entre otros) tienen como objetivo definir qué mantenimiento debe realizarse sobre los activos, resulta clave analizar la componente técnica del tipo de mantenimiento que evaluamos. Con esto nos referimos a si es físicamente posible realizar un dado tipo de mantenimiento. Esto dependerá de las características del modo de falla (el proceso que desembocará en la falla del activo) y las características de la tarea de mantenimiento a realizarse.
Con este primer párrafo sacamos una conclusión muy importante: “El mantenimiento a ejecutar sobre un activo depende, en parte, del comportamiento de los modos de falla y del tipo de tarea de mantenimiento”.
“El mantenimiento a ejecutar sobre un activo depende, en parte, del comportamiento de los modos de falla y del tipo de tarea de mantenimiento”.
Como corolario, identificamos dos puntos que deben estar presentes para poder evaluar la factibilidad técnica del mantenimiento:
- Deben estar registrados los modos de falla del sistema/componente analizado
- El Equipo de trabajo debe tener conocimiento de las alternativas de técnicas de mantenimiento a utilizar
Tipos de mantenimiento
No es el objetivo del presente documento brindar una guía exhaustiva sobre las diferentes estrategias de mantenimiento que podemos encontrar (existen libros y Normas escritas sobre el tema), sino sentar las bases para poder avanzar en el análisis de las variables que tenemos que considerar al analizar si es técnicamente factible un tipo de tarea de mantenimiento.
Es por ello que nos vamos a basar en la clasificación realizada por John Moubray en su Libro “RCM2 – Mantenimiento centrado en Confiabilidad”.
Dentro de las tareas proactivas (aquellas tareas que permiten accionar para evitar o minimizar las consecuencias de la falla) encontramos las siguientes:
- Tareas a condición o Mantenimiento Predictivo: Consiste en la medición de un parámetro (presión, temperatura, caudal, nivel, etc.) y el activo se deja en funcionamiento “a condición” de que no hayamos llegado al punto de lo que se conoce como “Falla potencial” (una vez comenzado el proceso hacia la falla funcional, sería el momento en el cual podemos tomar conocimiento de que estamos camino hacia la falla). Ejemplo: Inspección con termografía (reemplazo de componente si la temperatura se encuentra por encima de un valor definido).
- Reacondicionamiento/Sustitución cíclica o Mantenimiento Preventivo: Consiste en la reparación o reemplazo de un componente antes de su vida útil (momento en el cual comienza a aumentar la probabilidad condicional de que falle). Ejemplo: Reemplazo de filtro a los 3 meses de funcionamiento.
Tareas a condición / Mantenimiento Predictivo
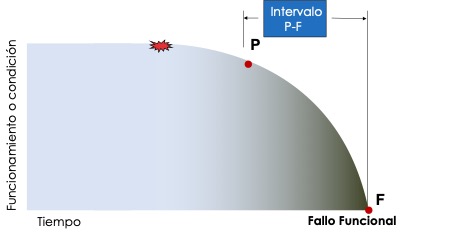
El mantenimiento predictivo se basa en la existencia de un aviso de que el activo/componente va a fallar antes de que ocurra la falla funcional “F” (momento en el cual el activo no hace más lo que queremos que haga). Estos avisos pueden tener, entre otras, las siguientes formas: temperatura, presión, caudal, nivel, vibraciones, ruido, etc.
Una vez que comienza a ocurrir el proceso hacia la falla, llamamos “P: Falla Potencial” al momento en el cual podemos entrar en conocimiento de que el activo fallará si no hacemos nada para impedirlo. ¿Qué serían en la práctica estos “puntos P”? Por ejemplo, el nivel de vibraciones que nos indica que los rodamientos van a fallar, la temperatura del tablero eléctrico que nos indica que existen puntos calientes o el nivel de aceite que nos da una idea que tenemos que rellenarlo.
Entonces, el mantenimiento predictivo consiste en chequear si existen fallas potenciales de manera tal que se pueda actuar para prevenir o evitar las consecuencias de la falla funcional.
El mantenimiento predictivo consiste en chequear si existen fallas potenciales de manera tal que se pueda actuar para prevenir o evitar las consecuencias de la falla funcional.
En esta línea, podemos afirmar que es técnicamente factible realizar una tarea a condición si se dan las siguientes condiciones:
- Existe un Punto P (falla potencial)
- El intervalo de tiempo entre el punto P y el punto F (denominado “Intervalo P-F) es suficientemente largo como para permitirnos actuar y evitar llegar al punto F, siendo este intervalo consistente.
- Es posible monitorear el elemento/componente a intervalos menores al intervalo P-F
Tareas a condición y patrones de falla
Si releemos las tres condiciones del párrafo anterior, veremos que en ninguna nombra a un patrón de falla en particular (aleatorio, vida útil, etc.). Esto es debido a que la factibilidad técnica del mantenimiento predictivo gira en torno a la existencia y características del Punto P y su intervalo P-F y no guarda relación alguna con la vinculación existente entre el modo de falla y la variable tiempo.
El mantenimiento predictivo, a diferencia de lo que ocurre con el mantenimiento preventivo, puede ser aplicado en cualquier tipo de patrón de falla
Dicho de otra manera, al mantenimiento predictivo no le interesa en qué momento empieza a ocurrir el proceso hacia la falla, sino que dicho proceso nos dé un aviso (punto P) y tenga un intervalo P-F que sea práctico.
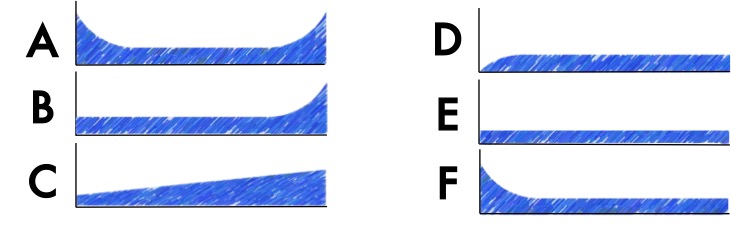
Esta definición es muy potente ya que podemos afirmar que el mantenimiento predictivo, a diferencia de lo que ocurre con el mantenimiento preventivo, puede ser aplicado en cualquier tipo de patrón de falla (vinculados con la vida útil o aleatorios, si los dividimos en dos grupos generales).
Mantenimiento Predictivo y la Industria 4.0
Sin dudas, de todos los tipos de mantenimiento existentes, el que más ha evolucionado es el mantenimiento predictivo. En la medida en que la tecnología avanza (hoy en auge a través de la llamada “Industria 4.0”), surgen tecnologías de mantenimiento predictivo que permiten anticiparnos cada vez más a las fallas o simplificar/facilitar el monitoreo de variables.
Ejemplos de esto son los drones que permiten una inspección visual en lugares inaccesibles o de difícil acceso para las personas, o sensores en tiempo real que se colocan en las máquinas y envían los resultados de las mediciones on-line.
Conocer las tecnologías de mantenimiento predictivo es importante. No obstante, no debe confundirse la tecnología con la decisión de qué mantenimiento realizar. No debemos perder de vista que debe ser el personal de la empresa (aquellos que más saben sobre los activos y su contexto operacional) el que tiene que evaluar el mantenimiento a realizar y realizarse las preguntas pertinentes, vinculadas a la factibilidad técnica (lo que hemos visto en este artículo) y la conveniencia (costo-eficacia) de realizarlo.